Technology
Synthetic Blending Component Process Overview
1. Feedstock Selection: The first step in making sustainable aviation fuel is selecting the appropriate feedstock. New Rise can use either corn oil or soybean oil as its primary feedstocks.
2. Pre-treatment: The feedstock is pre-treated through a ‘degumming’ process which removes phosphatides as well as any other any impurities such as trace metals. This ensures that the feedstock used by the facility is high quality, meets required specifications, and maximizes reactor catalyst life.
3. Hydrotreating: The pre-treated feedstock is then heated to high temperature and mixed with hydrogen gas in the presence of a catalyst to undergo hydrotreating. The objective of hydrotreating is to deoxygenate renewable lipids in the presence of hydrogen to produce linear paraffins.
4. Hydroisomerization: The next step in making sustainable aviation fuel involves hydroisomerization, which is the process of adding hydrogen to the product to improve its cold-flow properties. The objective of hydroisomerization is to upgrade the linear paraffins produced in the hydrotreating process into real drop-in middle distillate bio-based fuel.
5. Fractionation: After isomerization, the mixture is then fractionated to separate the different components of the fuel based on their boiling points. This allows for the separation of different compounds and ensures that the final product meets the required fuel specifications for synthetic blending component for producing SAF.
All Experienced Process Manufacturers with Proven Technologies
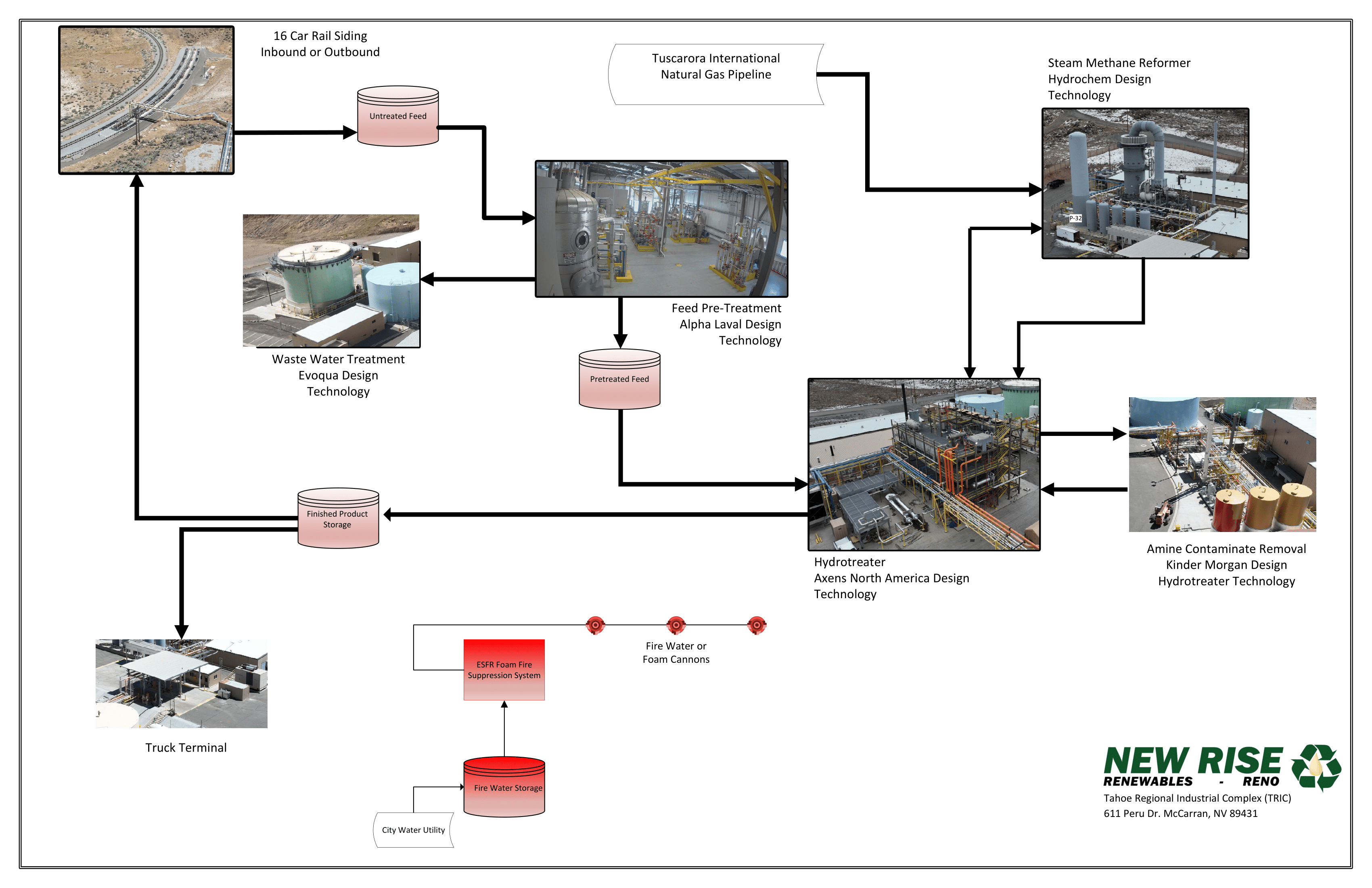
Feedstock Pretreatment Unit
Alfa Laval Equipment and Process Design
Founded in 1883, Alfa Laval is a global leader in renewable feedstock pretreatment systems.
- Ability to handle multiple types of feedstocks
- Low energy consumption
- Deep removal of phosphorous and free fatty acids, for the highest feedstock quality and maximizing catalyst life
Steam Methane Reformer (SMR)
Linde-Hydrochem
Founded in 1879, Linde is a global leader in the production, processing, storage and distribution of hydrogen.
Produces hydrogen for the hydrotreater.
- Excess steam from the SMR is routed to a steam turbine/generator, producing 500 KW of power to offset facility electricity consumption and to recycle water used in the process
- Optimized plant design to reduce energy costs
- Fully automated with fail-safe controls allowing unattended operation
- Energy recovery of propane from hydrotreater
Hydrotreating and Catalyst Provider
Axens North America
Founded in 2001, Axens is a leading provider of technologies to convert biomass into biofuels.
Converting triglycerides into:
- Renewable Synthetic Blending Component
- Renewable Naphtha
- Propane
- Propane that is produced is recycled back to the SMR and used as feedstock
- Minimizes CO2 formation and maximizes product yield
- Multi-year cycle lengths using a robust catalyst system
- Industry-leading reactor heat management system resulting in reduced reactor sizing
- Manages pressure drop utilizing HyClean® reactor internals and process scheme
- Full feedstock flexibility without modifications
- Full feedstock utilization flexibility without needing physical modifications to equipment
- Full cold flow property flexibility
Amine Gas Treating
Kinder Morgan
- Removal of contaminant gases including hydrogen sulfide (H2S) and carbon dioxide (CO2) from hydrotreater process stream
Waste Water Treatment
Evoqua Water Technologies
- Highly efficient and low cost anaerobic waste water treatment
- Safe to discharge to sewer once treated
- Minimal hazardous waste produced