Inside the SAF Production Process
Inside the SAF Production Process: How New Rise Renewables Helps Create Clean, Sustainable Aviation Fuel
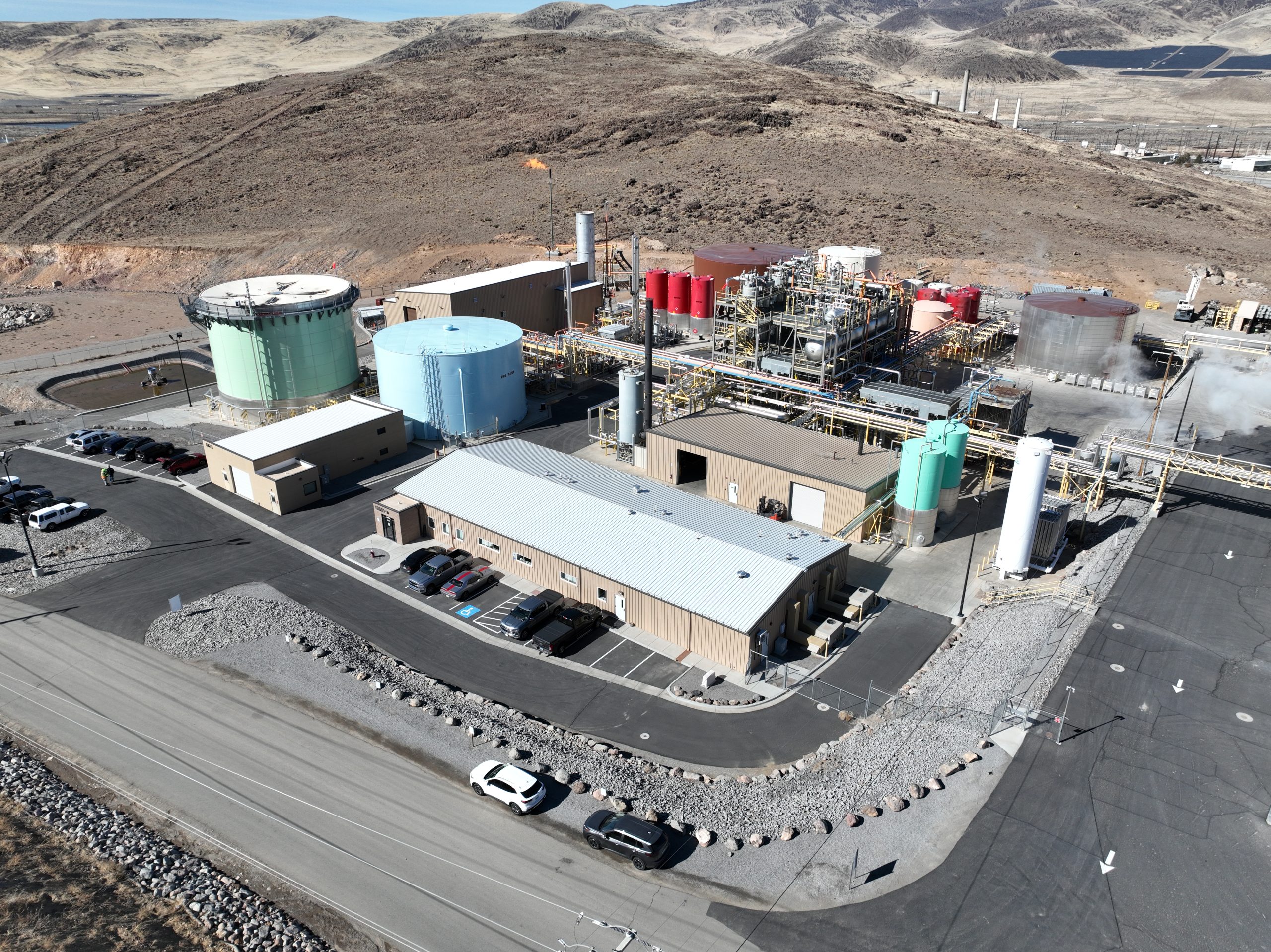
Sustainable Aviation Fuel (SAF) represents the future of aviation as the industry transitions toward greener solutions to combat climate change. At New Rise Renewables, our mission is to help provide cleaner, more efficient aviation fuel that significantly reduces greenhouse gas emissions. SAF, made from biomass and renewable feedstocks, is a direct substitute for conventional jet fuel but with a much smaller carbon footprint. In this blog, we will dive deep into the SAF production process, specifically focusing on the hydrotreating technology used at our facility to produce renewable synthetic blending component (SBC) needed for this fuel.
Understanding Sustainable Aviation Fuel (SAF)
Before we break down the production process, it is essential to grasp what SAF is and why it’s such a critical development in aviation. SAF is derived from renewable sources like vegetable oils. Unlike conventional jet fuel, which is refined from crude oil, SAF reduces life-cycle carbon emissions by up to 80%.
A critical advantage of SAF is that it can be used in existing aircraft without needing to make any engine modifications, making it an attractive, ready-to-deploy solution for reducing aviation’s carbon footprint.
SAF Production Overview: How SAF is Made
The production of SAF involves converting renewable biomass or waste feedstocks into liquid hydrocarbons that mimic conventional jet fuel’s performance. New Rise Renewables uses hydrotreating, a widely recognized refinery process, for producing the blending component for SAF that offers scalability, efficiency, and high-quality results.
While other processes such as the Fischer-Tropsch (FT) method are also used to produce SAF, we will focus on hydrotreating, as it is the core of our operation.
What is Hydrotreating? A Look at the Key SAF Production Process
Hydrotreating is a refining process that involves the use of hydrogen to remove contaminants like sulfur, nitrogen, and oxygen from the biomass feedstock. It converts organic oils and fats into hydrocarbons similar to those found in fossil fuels. Here is a closer look at the step-by-step process involved in hydrotreating:
- Feedstock Collection and Pre-Treatment
The first step in the renewable synthetic blending component (SBC) for SAF production process is the collection and pre-treatment of feedstocks. New Rise Renewables Reno uses exclusively non-food stock crops such as corn oil and soybean oil in its renewable process. These materials are pre-treated to remove impurities and contaminants that could reduce the effectiveness of reactor catalyst, and adversely effect the efficiency of the hydrotreating process.
- Hydrotreating Reaction: Conversion of Feedstock to Hydrocarbons
Once the feedstock has been pre-treated, it is introduced into the hydrotreator reactors. Here, the feedstock is exposed to hydrogen gas at high pressure and temperature in the presence of a catalyst. This reaction breaks down the molecular structure of the fats and oils, converting them into hydrocarbons that closely resemble conventional jet fuel components.
Key reactions in this process include:
- Deoxygenation: Removing oxygen from the feedstock, producing water as a by-product.
- Hydrogenation: Saturating carbon-carbon double bonds with hydrogen to stabilize the molecules.
The resulting product is a mix of hydrocarbons, which after further refinement, can meet the stringent cold-pour specifications of aviation fuels.
- Separation and Refining: Tailoring the Hydrocarbon Profile
After hydrotreating, the mixture of hydrocarbons undergoes a series of separation and refining steps to achieve the desired product compositions. The blending component for SAF produced from this process contains the same molecular structure as conventional jet fuel, but is made with a much smaller carbon footprint.
- Blending and Certification: Ready for Takeoff
Once SBC is produced, it undergoes rigorous testing to ensure it meets regulatory and safety standards. SBC is then blended with conventional jet fuel in varying ratios. Current regulations allow up to 50% SBC to be blended with conventional jet fuel to ultimately make SAF, ensuring it can be seamlessly used in today’s jet engines without any modifications.
After passing quality control, the SAF is ready to be delivered to airports and airlines, providing an immediate reduction in the aviation industry’s carbon footprint.
The Benefits of Hydrotreating
- Scalability and Efficiency
Hydrotreating technology is proven and highly scalable, making it well-suited for commercial-level SAF blending component. This is crucial for meeting the growing demand for sustainable fuels in the aviation industry.
- Product Quality
SAF blending component produced via hydrotreating is virtually indistinguishable from conventional jet fuel in terms of performance, meaning it can be used in today’s aircraft without any modifications to jet engines. The process also enables precise control over the fuel’s final properties, ensuring it meets the stringent requirements of the aviation sector.
- Emissions Reduction
SAF produced from blending of SBC with conventional jet fuel has a significantly lower environmental impact than traditional fossil-based jet fuel. It reduces greenhouse gas emissions by up to 80% over the fuel’s lifecycle, contributing to more sustainable aviation.
Hydrotreating vs. Other SAF Production Processes
While hydrotreating is a proven and highly effective method for producing the renewable blending component for SAF, it is not the only process available. Other methods, like the Fischer-Tropsch (FT) process, use a gasification technique to convert biomass into synthetic fuels. However, FT requires more complex infrastructure and processing, large amounts of power, and can be less flexible in terms of feedstock variety that it can utilize.
Hydrotreating, on the other hand, offers a more straightforward and efficient process that is scalable for industrial production and can easily adapt to using various feedstocks types.
The Future of SAF and New Rise Renewables
As the demand for sustainable aviation solutions continues to grow, the role of SAF will become even more critical in reducing the carbon footprint of the aviation industry. At New Rise Renewables, we are committed to the advancement of SAF production technology, and, its growth on a larger scale, all while helping to make aviation more sustainable.
We are continuously researching new feedstock sources, improving production efficiencies, and working with partners across the aviation industry to promote SAF adoption.